OPPORTUNITY DIAGNOSTIC
HOME / SOLUTIONS / OPPORTUNITY DIAGNOSTICS
COST AND LOSS PRIORITIZATION
The purpose of this solution is to identify opportunity areas to reduce Transformation Cost and Total Production Cost of the Plant. It is composed of the following activities:
Interviews.
Finance data collection, using the ERP: SAP, Oracle, AS400, etc.
Material and Labor Losses Analysis (ERP data).
Time Losses Identification (24 h balances).
Shop Floor Mas Balances.
Improvement Projects and solution to implement.
Savings Calculation and Cost Reductions.
Return of Investment.
Duration: 2-3 weeks.
The Opportunity Diagnostic guides the improvement efforts to the Plant Cost Reduction.
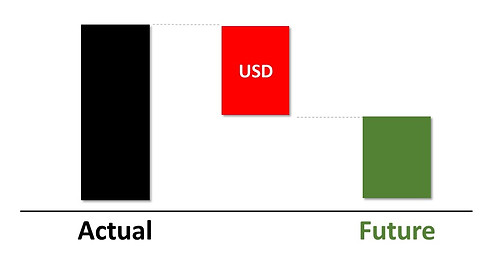
Benefits
Opportunity Identification to reduce Production Cost and increase the Plant Output.
Activity Based Costing Report (ABC).
Time / Material Losses Finance Calculation.
Cost and Savings Forecast.
Data Collection System Assessment.
Further Solutions
Some of the solutions that can be proposed to reduce Costs after an Opportunity Diagnostic are:
TPM.
Focused Improvement and Daily Management System can bring short term benefits (less than 1 year). TPM would give long term significant results.